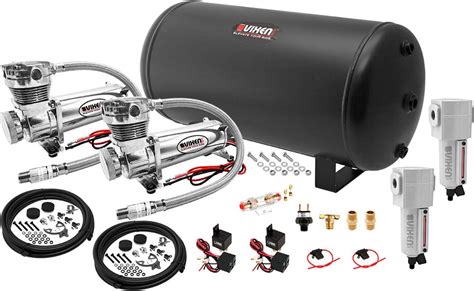
If you own or operate a truck, you may have heard of a truck air bag compressor. But what exactly is it and why is it important? In this blog post, we will explore the world of truck air bag compressors, including how they work, the different types available, and the factors to consider when choosing one. We will also discuss the benefits of using a truck air bag compressor, as well as common issues that may arise and maintenance tips to keep it in top condition. Lastly, we will provide troubleshooting tips for any problems you may encounter with your truck air bag compressor. So let’s dive in and discover everything you need to know about this essential truck accessory.
What is a truck air bag compressor?
A truck air bag compressor is a crucial component of a vehicle’s air suspension system. It is responsible for maintaining the air pressure in the air bags, which helps to support the weight of the truck and provide a smooth ride. Without a functioning compressor, the air bags would not be able to inflate and deflate properly, leading to an unstable and uncomfortable driving experience.
One of the main functions of a truck air bag compressor is to fill the air bags with compressed air. When the air bags need to be inflated, the compressor pumps air from the surrounding environment into the air bags. This increases the air pressure inside the bags, providing the necessary support for the truck. On the other hand, when the air bags need to be deflated, the compressor releases the compressed air, reducing the air pressure and allowing the truck to lower its suspension.
There are several types of truck air bag compressors available in the market. The most common types include single-path compressors, which have one air path for both inflating and deflating the air bags, and dual-path compressors, which have separate air paths for inflating and deflating. Additionally, some compressors come with built-in air tanks, which store compressed air for immediate use.
- Efficiency: Consider the efficiency of the compressor in terms of how quickly it can inflate and deflate the air bags.
- Noise level: Some compressors can be quite noisy, so it’s important to choose one that operates quietly.
- Compatibility: Ensure that the compressor is compatible with your truck’s air suspension system and can provide the necessary air pressure for your specific needs.
Advantages | Disadvantages |
---|---|
Improves ride comfort | Can be expensive to repair or replace |
Enhances vehicle stability | Requires regular maintenance |
Allows for adjustable suspension | Potential risk of air leaks |
In conclusion, a truck air bag compressor plays a vital role in maintaining the functionality of a vehicle’s air suspension system. It inflates and deflates the air bags to provide support, stability, and an adjustable ride height. When choosing a compressor, it’s important to consider factors such as efficiency, noise level, and compatibility. Although there are some maintenance and potential issues associated with truck air bag compressors, the benefits outweigh the drawbacks, making them a valuable component for truck owners.
Why is a truck air bag compressor important?
Truck air bag compressors play a crucial role in the functioning of a vehicle’s air suspension system. These devices are responsible for maintaining the optimal air pressure within the air bags, ensuring a smooth and comfortable ride. Without a properly functioning air bag compressor, the air suspension system would not be able to perform its intended functions, leading to reduced ride quality and potential safety hazards.
One of the main reasons why a truck air bag compressor is important is its ability to adjust the vehicle’s suspension level according to the load it is carrying. Whether the truck is empty or fully loaded, the air bag compressor ensures that the suspension system adapts to provide the best possible stability and control. This is particularly important for trucks that carry heavy loads or tow trailers, as it helps to maintain proper weight distribution and prevents the vehicle from sagging or bouncing excessively.
Furthermore, a functioning air bag compressor contributes to the overall longevity of the truck’s suspension system. By keeping the air springs adequately pressurized, it helps to distribute the weight evenly across the suspension components, reducing the strain on individual parts. This not only extends the lifespan of the suspension system but also minimizes the risk of premature wear and tear, leading to potential costly repairs in the future.
Aside from enhancing ride quality and promoting vehicle longevity, a truck air bag compressor also plays a crucial role in ensuring safety on the road. By maintaining the proper suspension height, it helps to improve stability and handling, especially during sudden turns, maneuvers, or emergency situations. A truck with a well-functioning air bag compressor is less prone to rollovers, swaying, and other instability issues, providing the driver with better control and confidence behind the wheel.
In summary, a truck air bag compressor is important for several reasons. It not only enhances ride quality and driver comfort but also contributes to the longevity of the suspension system and ensures road safety. By maintaining the optimal air pressure within the air bags, the air bag compressor enables the vehicle to handle varying load conditions and provides stability and control. Therefore, it is important to invest in a high-quality truck air bag compressor and ensure regular maintenance to enjoy these benefits for a long time.
How does a truck air bag compressor work?
A truck air bag compressor is an essential component of a truck’s air suspension system. It is responsible for inflating and deflating the air bags that support the weight of the truck and provide a smoother ride. The compressor works by using a motor-driven piston to compress air and then deliver it to the air bags. In this blog post, we will explore the inner workings of a truck air bag compressor and understand how it performs its important role in a truck’s suspension system.
At the heart of a truck air bag compressor is the motor, which is powered by the truck’s electrical system. The motor drives a piston that moves up and down within a cylinder. As the piston moves downward, it creates a vacuum that draws air into the compressor. Once the piston reaches the bottom of its stroke, it begins to move upward, compressing the air inside the cylinder. The compressed air is then stored in a reservoir tank until it is needed by the air bags.
When the truck’s suspension system detects a need for additional air in the air bags, such as when the truck is carrying a heavy load, it sends a signal to the compressor to start delivering compressed air. This signal activates an internal valve in the compressor, allowing the compressed air to flow from the reservoir tank to the air bags. The air bags then inflate, providing the necessary support to the truck’s suspension system.
Conversely, when the truck needs to reduce the amount of air in the air bags, such as when the load is lighter or the truck is unladen, the suspension system sends a signal to the compressor to stop delivering compressed air. The internal valve in the compressor closes, preventing the air from flowing to the air bags. As a result, the air bags deflate, allowing the truck’s suspension system to adjust to the desired ride height.
In summary, a truck air bag compressor works by using a motor-driven piston to compress air and deliver it to the air bags. It functions in response to signals from the truck’s suspension system, inflating or deflating the air bags as needed to maintain the proper ride height and support the weight of the truck. Its reliable operation is crucial for ensuring a smooth and comfortable ride, as well as maintaining the integrity of the truck’s suspension system.
Types of truck air bag compressors
When it comes to truck air bag compressors, there are several types to choose from based on the specific needs and requirements of your truck. Each type has its own unique features and advantages, making it important to understand the different options available. In this blog post, we will explore the various types of truck air bag compressors and how they can benefit your truck’s air suspension system.
1. Single Path Compressor: This type of air bag compressor is the most common and basic option available. It consists of a single compressor that supplies air to all four air bags simultaneously. While it is a simple and cost-effective choice, it may not provide as precise control over each air bag as other types.
2. Dual Path Compressor: A dual path compressor, also known as a dual pack compressor, consists of two separate compressors that are designed to provide individual control over each air bag. This allows for more precise adjustments and customization of the air suspension system. It is a popular choice among truck owners who want enhanced performance and control.
3. Heavy-Duty Compressor: As the name suggests, a heavy-duty compressor is designed for trucks that carry heavy loads or tow trailers. These compressors are capable of providing a higher volume and pressure of air, ensuring optimal performance even under heavy load conditions. They are built to withstand the demands of heavy-duty applications and are typically more durable and long-lasting.
These are just a few examples of the types of truck air bag compressors available on the market. It is important to consider factors such as load capacity, desired level of control, and intended usage before making a decision. By choosing the right type of air bag compressor for your truck, you can ensure a smooth and comfortable ride, improved handling, and enhanced safety.
Type of Compressor | Advantages |
---|---|
Single Path Compressor | Simple and cost-effective |
Dual Path Compressor | Individual control over each air bag |
Heavy-Duty Compressor | Higher volume and pressure for heavy loads |
Choosing the right type of truck air bag compressor is crucial for optimizing the performance and reliability of your truck’s air suspension system. Consider the specific requirements of your truck and consult with a professional if needed to make an informed decision. With the right compressor, you can enjoy a smoother and more controlled ride, improved load-carrying capabilities, and increased overall safety on the road.
Factors to consider when choosing a truck air bag compressor
When it comes to choosing a truck air bag compressor, there are several important factors to consider. The right compressor can make all the difference in the performance and safety of your truck’s air bag suspension system. Here are some key considerations to keep in mind:
1. Compatibility: Make sure the compressor you choose is compatible with your specific truck make and model. Different trucks may require different air bag compressors, so it’s crucial to check the compatibility before making a purchase. This will ensure proper fitment and optimal performance.
2. Performance: Consider the performance capabilities of the compressor. Look for features such as maximum air pressure, flow rate, and duty cycle. These factors will determine how efficiently the compressor can fill and maintain pressure in the air bags, allowing for smoother rides and better control.
3. Quality and Durability: Check the quality and durability of the compressor. Look for reputable brands known for producing reliable and long-lasting products. Read customer reviews and ratings to get an idea of the compressor’s overall performance and durability.
4. Noise Level: Depending on your preference, you may want to consider the noise level of the compressor. Some compressors operate quietly, while others may produce noticeable noise. This can be important if you frequently drive in quieter areas or if noise is a concern for you.
5. Ease of Installation: Consider the ease of installation. Look for a compressor that comes with clear instructions and all the necessary hardware for a straightforward installation process. If you’re not familiar with automotive installations, you may want to opt for a compressor that is relatively easy to install or consider professional installation.
6. Price and Warranty: Lastly, consider the price and warranty of the compressor. Compare prices from different retailers to ensure you’re getting the best deal. Additionally, check the warranty coverage provided by the manufacturer. A longer warranty period can provide peace of mind and protect your investment.
By considering these factors when choosing a truck air bag compressor, you can ensure that you select the right one for your needs. Remember, the compressor plays a crucial role in maintaining proper air pressure in the air bags, so it’s important to choose wisely for optimal performance and safety.
Benefits of using a truck air bag compressor
A truck air bag compressor is an essential component of a truck’s air suspension system. It plays a crucial role in maintaining the level of the truck’s suspension and providing a smooth and comfortable ride. But besides these basic functions, there are various benefits of using a truck air bag compressor.
One of the significant benefits of using a truck air bag compressor is enhanced load-carrying capacity. With the help of an air suspension system, the truck can adjust its height and level based on the weight of the load it is carrying. This feature ensures that the truck remains stable and balanced, even when carrying heavy loads.
Another advantage of using a truck air bag compressor is improved ride quality. The air suspension system, along with the compressor, absorbs shocks and vibrations, resulting in a smoother and more comfortable ride for the driver and passengers. This is especially beneficial when traveling long distances or driving on rough terrains.
Additionally, a truck air bag compressor can contribute to better fuel efficiency. By maintaining the level of the truck’s suspension and preventing it from sagging, the compressor helps reduce drag and wind resistance. This, in turn, can lead to improved fuel economy, saving costs and reducing the carbon footprint of the truck.
Common issues with truck air bag compressors
A truck air bag compressor is an essential component of the air suspension system in a truck. It is responsible for inflating and deflating the air bags in order to provide a smooth and comfortable ride. However, like any other mechanical device, truck air bag compressors can experience common issues over time. It is important to be aware of these issues and know how to address them in order to maintain the optimal performance of the air suspension system.
One of the most common issues with truck air bag compressors is air leakage. This can occur due to a variety of reasons, such as worn-out seals, damaged air lines, or loose fittings. When there is air leakage, the compressor has to work harder to maintain the desired air pressure, which can lead to overheating and reduced efficiency. It is important to regularly inspect the air lines and fittings for any signs of damage or looseness. Additionally, replacing worn-out seals and tightening loose fittings can help prevent air leakage issues.
Another common issue is compressor failure. This can happen due to various factors, such as age, excessive strain on the compressor, or lack of proper maintenance. When a compressor fails, it can result in the air suspension system not being able to maintain the desired air pressure. This can lead to a bumpy and uncomfortable ride. Regular maintenance, such as checking the compressor for any abnormal noises or vibrations, and ensuring that it is properly lubricated, can help prevent compressor failure.
Electrical problems can also be a common issue with truck air bag compressors. This can include issues with the wiring, relays, or switches that control the compressor. When there are electrical problems, the compressor may not receive the necessary power to operate effectively. It is important to regularly inspect the electrical components and connections, and replace any faulty wiring or components to ensure the proper functioning of the compressor.
- Air leakage: Regularly inspect air lines and fittings for damage or looseness. Replace worn-out seals and tighten loose fittings.
- Compressor failure: Check the compressor for any abnormal noises or vibrations. Ensure proper lubrication and regular maintenance.
- Electrical problems: Inspect electrical components and connections. Replace faulty wiring or components.
Common Issues | Solutions |
---|---|
Air leakage | Inspect air lines and fittings. Replace seals and tighten fittings. |
Compressor failure | Regularly maintain and lubricate the compressor. Check for abnormal noises or vibrations. |
Electrical problems | Inspect electrical components and connections. Replace faulty wiring or components. |
In conclusion, it is important to be aware of the common issues that can arise with truck air bag compressors in order to prevent any inconvenience or potential damage. By addressing air leakage, compressor failure, and electrical problems, truck owners can ensure the optimal performance and longevity of their air suspension system. Regular maintenance and inspections are key to identifying and resolving these issues before they escalate. Remember to consult a professional if you are unsure or need further assistance in maintaining or troubleshooting your truck air bag compressor.
Maintenance tips for truck air bag compressors
Truck air bag compressors are essential components of a vehicle’s suspension system, responsible for maintaining the proper air pressure in the air bags. Regular maintenance of these compressors is crucial to ensure their optimal performance and maximize their lifespan. This blog post aims to provide some valuable maintenance tips for truck air bag compressors so that you can keep them working efficiently.
Firstly, it is important to regularly inspect the air lines and fittings connected to the compressor. Over time, these components may deteriorate due to wear and tear or exposure to harsh weather conditions. Look for any signs of cracks, leaks, or loose connections. If you notice any issues, promptly replace or repair the affected parts to prevent air leakage, which can negatively impact the performance of the compressor.
Secondly, **regularly check and clean the air filter** of the compressor. The air filter prevents dirt, debris, and other contaminants from entering the compressor and causing damage. Depending on the manufacturer’s recommendations, you may need to clean or replace the filter every few months or so. A clogged or dirty air filter can restrict airflow and reduce the efficiency of the compressor, so be sure to keep it clean.
Lastly, **keep the compressor lubricated** to ensure smooth operation. Most compressors have specific lubrication requirements, so refer to the manufacturer’s guidelines for the recommended lubricant and frequency of lubrication. Regularly apply the recommended lubricant to the compressor’s moving parts, such as the piston and cylinder. This will help reduce friction, prevent overheating, and extend the lifespan of the compressor.
Following these maintenance tips will not only help you avoid costly repairs but also enhance the overall performance and reliability of your truck air bag compressor. By keeping the air lines and fittings in good condition, cleaning the air filter regularly, and ensuring proper lubrication, you can ensure that your compressor operates efficiently and effectively for a long time to come.
In summary, maintaining truck air bag compressors is essential to optimize their performance and extend their lifespan. Regularly inspecting the air lines and fittings, cleaning or replacing the air filter, and lubricating the moving parts are key maintenance tasks. By following these simple tips, you can experience smoother rides and improved suspension performance with your truck’s air bag compressor.
Troubleshooting problems with truck air bag compressors
Truck air bag compressors are an essential component of the air suspension system in commercial trucks. They provide the necessary air pressure to inflate and deflate the air bags, which support the weight of the truck and provide a smoother ride. However, like any other mechanical system, truck air bag compressors can experience issues that may affect their performance. In this blog post, we will discuss some common problems that can occur with truck air bag compressors and provide troubleshooting tips to help you address these issues effectively.
One of the most common problems with truck air bag compressors is insufficient air pressure. A truck may experience a gradual loss of air pressure over time, leading to poor suspension performance and an uncomfortable ride. This problem can be caused by leaks in the air lines or fittings, a faulty compressor, or worn-out air bags. To troubleshoot this issue, start by checking for any visible signs of air leaks, such as hissing sounds or air bubbles. Replace any damaged air lines or fittings and tighten loose connections.
Another common problem is excessive noise coming from the air compressor. If you notice unusual noises, such as grinding, rattling, or squealing, it could indicate a problem with the compressor’s motor or bearings. This could be due to improper lubrication, worn-out components, or motor failure. Check the compressor’s oil level and add oil if necessary. If the noise persists, it may be necessary to replace the compressor or have it serviced by a professional.
- Insufficient air pressure: Check for air leaks, replace damaged air lines or fittings, and tighten loose connections.
- Excessive noise: Check the compressor’s oil level, add oil if necessary, and consider replacing or servicing the compressor.
- Inconsistent suspension performance: Inspect the air bags for signs of wear or damage, and replace them if necessary. Also, check the compressor’s pressure switch and adjust it if needed.
- Compressor not turning on: Check the power supply to the compressor, replace any blown fuses, and ensure the compressor is properly grounded. If the issue persists, have the electrical system and wiring inspected by a professional.
In summary, troubleshooting problems with truck air bag compressors requires careful inspection and identification of the underlying issues. By addressing common problems such as insufficient air pressure, excessive noise, inconsistent suspension performance, and compressor not turning on, you can ensure optimal performance and longevity of your truck’s air suspension system. Regular maintenance and prompt repairs are essential to avoid costly replacements and ensure a smooth and safe ride.
Frequently Asked Questions
What is a truck air bag compressor?
A truck air bag compressor is a device that is used to inflate and maintain air pressure in the air suspension system of a truck. It supplies pressurized air to the air bags or air springs, allowing them to support the weight of the vehicle and provide a smooth and comfortable ride.
Why is a truck air bag compressor important?
A truck air bag compressor is important because it helps to maintain the proper air pressure in the air suspension system, which is crucial for the stability, handling, and overall performance of the truck. It helps to distribute the weight evenly across all the tires, enhances the suspension’s ability to absorb road shocks, and allows for easy adjustment of the ride height.
How does a truck air bag compressor work?
A truck air bag compressor works by drawing in air from the atmosphere through an intake valve. This air is then compressed and stored in a reservoir tank. When the air pressure in the air bags drops below a certain level, the compressor is activated and it pumps air into the air bags to restore the desired pressure. The compressor is typically controlled by a pressure switch or a leveling system.
Types of truck air bag compressors
There are two main types of truck air bag compressors: portable compressors and onboard compressors. Portable compressors are smaller and can be easily moved and used for various applications. Onboard compressors, on the other hand, are permanently installed in the truck and are specifically designed for the air suspension system.
Factors to consider when choosing a truck air bag compressor
When choosing a truck air bag compressor, it is important to consider factors such as the maximum pressure and airflow capacity, compatibility with the truck’s air suspension system, power source (electric or engine-driven), durability, noise level, and ease of installation and operation.
Benefits of using a truck air bag compressor
Using a truck air bag compressor has several benefits, including improved ride quality, enhanced load-carrying capacity, better handling and stability, the ability to level the truck when towing or carrying heavy loads, increased fuel efficiency, and reduced wear and tear on other suspension components.
Common issues with truck air bag compressors
Some common issues with truck air bag compressors include air leaks, compressor failure, pressure switch malfunction, motor overheating, and excessive noise. Regular maintenance and timely repairs can help prevent these problems.
Maintenance tips for truck air bag compressors
To ensure the proper functioning and longevity of a truck air bag compressor, it is important to regularly inspect and clean the compressor, check for air leaks, maintain the proper oil level, replace worn-out components, and follow the manufacturer’s recommended maintenance schedule.
Troubleshooting problems with truck air bag compressors
If a truck air bag compressor is experiencing issues such as failure to inflate the air bags, loss of air pressure, or unusual noises, troubleshooting steps may include checking the power source, inspecting the air lines and fittings for leaks, examining the pressure switch, cleaning or replacing the intake filter, and consulting the manufacturer’s troubleshooting guide or seeking professional assistance.