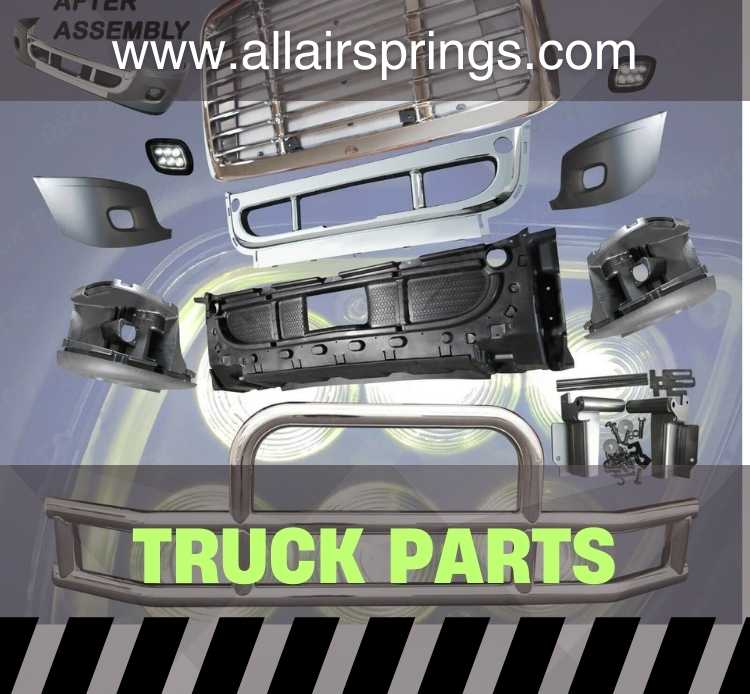
Air Springs: A Comprehensive Guide to Understanding, Designing, and Maintaining the Versatile Suspension System
Introduction to Air Springs
Air springs are an innovative suspension system that has been around for several decades. They offer a superior ride quality compared to traditional spring systems, making them a popular choice in various industries. In this chapter, we’ll introduce you to air springs and give you an overview of how they work.
Air springs, also known as air bags or air bellows, consist of a flexible rubber or polyurethane bladder that is filled with air. The bladder is connected to a valve that controls the amount of air pressure in the spring. When air is pumped into the bladder, it expands, creating a cushion of air that supports the weight of the vehicle or machinery it’s installed on.
One of the primary advantages of air springs is that they offer a smoother ride quality compared to traditional spring systems. The air cushion created by the bladder absorbs shocks and vibrations, providing a more comfortable ride for passengers and reducing the wear and tear on the vehicle or machinery.
Air springs are also highly customizable, as the amount of air pressure in the bladder can be adjusted to suit specific load requirements. This means that air springs can be used in a wide range of applications, from heavy-duty trucks to luxury cars to industrial machinery.
In the next chapter, we’ll take a closer look at the different types of air springs available and the pros and cons of each.
Types of Air Springs
There are several types of air springs available, each with its own set of advantages and disadvantages. In this chapter, we’ll take a closer look at the most common types of air springs and their applications.
-
Sleeve Air Springs: Sleeve air springs consist of a flexible rubber sleeve that surrounds a piston. When air is pumped into the sleeve, it expands and lifts the piston, creating a cushion of air. Sleeve air springs are commonly used in light-duty trucks, vans, and SUVs.
-
Convoluted Air Springs: Convoluted air springs, also known as bellows air springs, consist of a series of convoluted rubber or polyurethane bladders that are stacked on top of each other. When air is pumped into the bladders, they expand and compress, creating a cushion of air. Convoluted air springs are commonly used in heavy-duty trucks, buses, and trailers.
-
Rolling Lobe Air Springs: Rolling lobe air springs consist of a flexible rubber or polyurethane bladder that rolls along an axle as it expands and contracts. This rolling motion reduces friction and wear, making rolling lobe air springs a good choice for applications that require frequent cycling, such as heavy-duty trucks and trailers.
-
Double Convolute Air Springs: Double convolute air springs are similar to convoluted air springs, but they have two convoluted bladders stacked on top of each other. This design provides greater load capacity and stability, making double convolute air springs a good choice for heavy-duty applications.
Each type of air spring has its own set of advantages and disadvantages, depending on the application. In the next chapter, we’ll dive deeper into the design and construction of air springs.
Design and Construction of Air Springs
The design and construction of air springs play a crucial role in their performance and longevity. In this chapter, we’ll take a closer look at the components and factors that contribute to the design and construction of air springs.
The basic components of an air spring include the rubber or polyurethane bladder, the end plates that hold the bladder in place, and the piston that transfers the load to the bladder. The end plates are typically made of steel or aluminum and are designed to withstand the forces exerted on them by the bladder and piston.
The material used to construct the bladder is also an important factor in the design of air springs. Rubber and polyurethane are the most commonly used materials for air spring bladders due to their flexibility, durability, and resistance to wear and tear.
When designing an air spring, there are several factors that need to be taken into consideration, including load capacity, ride height, and spring rate. Load capacity refers to the maximum weight that the air spring can support, while ride height refers to the distance between the ground and the vehicle or machinery. Spring rate refers to the amount of force required to compress the air spring by a certain amount.
The shape and size of the air spring also play a role in its design and construction. Depending on the application, air springs can be cylindrical, rectangular, or custom-shaped to fit specific requirements.
Overall, the design and construction of air springs are critical to their performance and longevity. In the next chapter, we’ll explore tips for maintaining and repairing air springs to ensure their continued functionality.
Maintaining and Repairing Air Springs
Like any mechanical component, air springs require proper maintenance and occasional repairs to ensure their continued functionality. In this chapter, we’ll explore tips for maintaining and repairing air springs.
One of the most important maintenance tasks for air springs is keeping them clean and free from debris. Dirt and debris can cause premature wear and tear on the bladder and end plates, reducing the lifespan of the air spring. Regular cleaning with soap and water can help prevent this.
Another important maintenance task is checking the air pressure in the air spring regularly. Low air pressure can cause the air spring to bottom out, while high air pressure can cause it to overinflate, both of which can damage the air spring. Check the manufacturer’s recommended air pressure and adjust as needed.
If you notice any leaks or tears in the bladder, it’s important to address them promptly. Small leaks can often be repaired with a patch kit, while larger tears may require replacement of the entire bladder. It’s important to use the correct repair materials and techniques to ensure the repair is effective and long-lasting.
Regular inspections of the air spring and its components can also help identify potential issues before they become major problems. Check for signs of wear and tear, such as cracks or corrosion on the end plates, and replace any damaged components as needed.
In some cases, it may be necessary to replace the entire air spring. This is often the case if the air spring is significantly damaged or has reached the end of its lifespan.
By following these tips for maintaining and repairing air springs, you can ensure their continued functionality and longevity. In the next chapter, we’ll explore some of the common applications for air springs.
Applications of Air Springs
Air springs have a wide range of applications in various industries, from automotive and aerospace to construction and agriculture. In this chapter, we’ll explore some of the most common applications of air springs.
One of the most well-known applications of air springs is in automotive suspension systems. Air springs are often used in luxury cars and commercial trucks to provide a smoother ride and better handling. They can also be used to adjust the ride height of the vehicle for different driving conditions.
Air springs are also used in aerospace applications, particularly in aircraft landing gear. They provide a cushioning effect during landing and takeoff, helping to absorb the impact and reduce stress on the aircraft structure.
In the construction industry, air springs are used in heavy machinery such as cranes and excavators to provide stability and absorb shock. They can also be used in pile drivers and vibratory rollers to help compact soil and pavement.
In agriculture, air springs are often used in tractors and other farm equipment to provide a smoother ride and reduce wear and tear on the machinery. They can also be used in harvesters and planters to help distribute weight evenly and reduce soil compaction.
Other common applications of air springs include use in furniture and seating, such as office chairs and mattresses, as well as in medical equipment and industrial machinery.
Overall, air springs have a wide range of applications across various industries and provide a unique set of benefits, such as improved ride comfort, stability, and load-carrying capacity. As technology continues to advance, we can expect to see even more innovative uses for air springs in the future.
For detailed information, you can contact us at torqueusa.com.