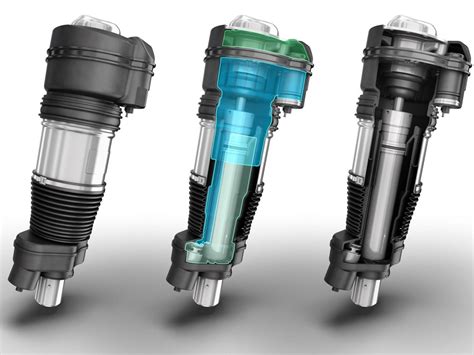
Introduction:
Air springs are a type of suspension system that has been gaining popularity due to their enhanced cushioning and adjustability. As an alternative to traditional springs, air springs utilize compressed air to support the weight of a vehicle, providing improved ride comfort and handling. In this blog post, we will delve into the mechanics of air springs, their various types, and the benefits they offer. We will also discuss their maintenance requirements, factors to consider when choosing air springs, as well as the installation and replacement processes. Whether you are looking to upgrade your vehicle’s suspension or simply curious about air springs, read on to discover everything you need to know.
What are air springs?
When it comes to vehicle suspension systems, air springs play a crucial role. Also known as airbags, air springs are inflatable devices that are designed to provide support and cushioning to vehicles. They are commonly used in heavy-duty trucks, buses, and recreational vehicles, but can also be found in passenger cars and motorcycles. Air springs are made from flexible and durable materials such as rubber and synthetic fabric, which enables them to withstand extreme pressures and provide a smooth and comfortable ride.
There are several key components that make up an air spring. Firstly, there is an airtight bladder that holds the compressed air. This bladder is typically made of rubber and is reinforced to handle the pressure. Secondly, there is an air valve that allows the air to enter and exit the air spring. This valve is used to adjust the pressure and maintain the desired ride height. Finally, there are mounting brackets that secure the air spring to the vehicle’s suspension system. These brackets ensure proper alignment and stability.
How do air springs work?
The concept of air springs is fascinating and widely used in various industries. Air springs, also known as airbags or pneumatic springs, are mechanical devices that use compressed air to provide shock absorption and support to vehicles or machinery. It works on the principle of air pressure and is composed of a flexible and airtight bag made of durable materials such as rubber or reinforced fabric.
An air spring consists of two main components—the air chamber and the piston. The air chamber is the flexible bag that holds the compressed air, while the piston is responsible for controlling the air flow and pressure within the chamber. When the air spring is installed and the vehicle is in motion, the weight and force exerted on the spring compress the air chamber, resulting in the suspension being raised or lowered according to the load and road conditions.
The mechanism of air springs involves a complex process of air compression and decompression. When the spring is compressed, the air inside the chamber becomes denser, leading to an increase in air pressure. This increased pressure then acts against the weight or force applied to the spring, providing a cushioning effect and absorbing shocks or vibrations.
Benefits of using air springs
Air springs, also known as airbags or air suspension, are a type of suspension system commonly used in vehicles. They are made of a flexible and durable rubber material that is inflated with compressed air. Air springs offer numerous benefits that make them a popular choice in various industries.
One of the key advantages of using air springs is their ability to provide a smooth and comfortable ride. The air inside the springs acts as a cushion, absorbing shocks and vibrations from the road. This not only enhances the driving experience for passengers but also helps to protect the vehicle and its components from damage caused by excessive jolts and impacts.
Additionally, air springs offer adjustable ride height and load-carrying capacity. This means that the level of the vehicle can be easily adjusted to suit different driving conditions or to accommodate varying loads. By simply increasing or decreasing the air pressure in the springs, the ride height can be controlled. This is particularly useful for vehicles that frequently carry heavy loads or operate in off-road environments where ground clearance may need to be increased.
Another benefit of air springs is their durability and resistance to wear and tear. The rubber material used in their construction is designed to withstand harsh conditions and heavy use. Unlike traditional coil or leaf springs, which can sag or deteriorate over time, air springs maintain their shape and performance for longer periods. This not only reduces the need for regular replacements but also helps to minimize maintenance and repair costs.
Furthermore, air springs can improve fuel efficiency and reduce environmental impact. By providing a smoother ride and better stability, they can enhance the overall efficiency of a vehicle. This, in turn, can lead to reduced fuel consumption and lower emissions. With the growing emphasis on sustainability and eco-friendly practices, using air springs can contribute to a greener transportation industry.
Benefits of Air Springs |
---|
Smooth and comfortable ride |
Adjustable ride height and load-carrying capacity |
Durability and resistance to wear and tear |
Improved fuel efficiency and reduced environmental impact |
In conclusion, air springs offer a range of benefits that make them a valuable component in various vehicles and applications. From providing a smooth and comfortable ride to offering adjustable ride height and load-carrying capacity, their versatility is highly advantageous. Additionally, their durability and resistance to wear and tear contribute to cost savings and reduced maintenance. Furthermore, the improved fuel efficiency and reduced environmental impact make air springs an attractive choice for those concerned with sustainability. Overall, incorporating air springs into a vehicle’s suspension system can greatly enhance performance and user experience.
Types of air springs
Air springs, also known as air suspension systems, are a type of vehicle suspension that uses air-filled rubber bags to provide a smoother and more comfortable ride. These springs are designed to replace traditional coil or leaf springs in a vehicle’s suspension system and offer several advantages over their counterparts. In this blog post, we will explore the different types of air springs available in the market and their unique characteristics.
1. Convoluted Air Springs: Convoluted air springs, also known as bellows or flexible member air springs, are the most common type of air springs used in commercial vehicles. These springs are made up of multiple layers of rubber with reinforcing layers, allowing them to withstand heavy loads and provide excellent ride quality. Convoluted air springs are commonly used in heavy trucks, buses, and RVs.
2. Rolling Lobe Air Springs: Rolling lobe air springs consist of an air chamber enclosed by a multi-ply rubber sleeve. These springs have a convoluted shape that provides progressive spring rate characteristics. Rolling lobe air springs are often used in passenger cars and light trucks, as they offer a smoother ride and improved handling.
3. Sleeve Air Springs: Sleeve air springs, also known as cylindrical air springs, are used in various industrial applications, such as machinery and equipment. These springs are constructed with a cylindrical-shaped rubber sleeve that provides a consistent spring rate throughout the suspension travel. Sleeve air springs are known for their durability and high load-carrying capacity.
Aside from these three main types, there are also other specialized air springs available for specific applications. Some examples include reversible sleeve air springs, reversible sleeve strut air springs, and triple convoluted air springs. Each type of air spring offers unique characteristics and benefits, making them suitable for different vehicles and uses.
- Improved ride comfort
- Adjustable suspension height
- More precise handling
- Reduced vibration and noise
- Extended tire life
- Reduced wear and tear on other suspension components
In summary, air springs come in various forms to cater to different vehicles and applications. Whether you are driving a heavy-duty truck, a luxury car, or operating industrial machinery, there is an air spring type that can enhance your vehicle’s performance and ride quality. The choice of air springs will depend on factors such as the vehicle’s weight, intended usage, and desired ride characteristics. By understanding the different types of air springs available, you can make an informed decision and enjoy the many benefits they offer.
Air springs vs. traditional springs
When it comes to choosing the right suspension system for your vehicle, you may have come across the terms “air springs” and “traditional springs.” Both of these options have their own set of advantages and disadvantages, and understanding the differences between them can help you make an informed decision. In this blog post, we will explore the key differences between air springs and traditional springs, and discuss their respective benefits and drawbacks.
1. Air Springs:
Also known as airbags, air springs are a type of suspension system that utilize compressed air to support the weight of a vehicle. These airbags are made from durable and flexible materials such as rubber or reinforced fabric. Air springs can be adjusted to different levels of stiffness or softness, allowing for greater flexibility in terms of ride comfort and load support. They are commonly used in heavy-duty vehicles like trucks and buses.
2. Traditional Springs:
On the other hand, traditional springs are mechanical systems that use metal coils or leaf springs to absorb shocks and maintain the vehicle’s height. They come in various designs and configurations, including coil springs, leaf springs, torsion bars, and more. Traditional springs have been used in vehicles for many years and are known for their reliability and durability.
3. Differences and Benefits:
Now that we have a basic understanding of air springs and traditional springs, let’s explore their differences and benefits:
- Ride Comfort: Air springs offer a smoother and more comfortable ride compared to traditional springs. The ability to adjust the air pressure allows for personalized comfort, reducing bumps and vibrations on various road surfaces.
- Load Support: Air springs excel in providing load support, especially in heavy-duty vehicles. By adjusting the air pressure, the suspension can accommodate different loads and maintain a level ride height, enhancing stability and control.
- Adjustability: One of the major advantages of air springs is their adjustability. You can vary the air pressure to customize the suspension according to your preferences, road conditions, or cargo load. Traditional springs, on the other hand, have a fixed stiffness and cannot be easily adjusted.
In conclusion, both air springs and traditional springs have their own unique advantages and applications. If you prioritize ride comfort, load support, and adjustability, then air springs may be the right choice for you. However, if you value simplicity, reliability, and cost-efficiency, traditional springs can still be a reliable option. It is essential to consider your specific needs, vehicle type, and intended usage before making a decision between these two suspension systems.
Common applications of air springs
Air springs, also known as airbags, are widely used in various industries and applications due to their unique characteristics and advantages. These pneumatic devices are designed to provide support, shock absorption, and isolation from vibrations. In this blog post, we will explore the common applications of air springs and how they are utilized in different environments.
1. Automotive Industry: One of the most common uses of air springs is in the automotive industry. They are often installed in vehicles to improve ride quality, stability, and comfort. Air springs can adjust the vehicle’s suspension system to adapt to different road conditions and loads. They are particularly used in luxury cars, trucks, buses, and recreational vehicles.
2. Industrial Machinery: Air springs play a significant role in various industrial applications. They are used as vibration isolators to dampen machine vibrations and reduce noise levels. Air springs can also be found in heavy machinery, such as presses, stamping equipment, and manufacturing systems, to provide support and prevent damage caused by dynamic loads and shock forces.
3. Heavy-Duty Vehicles and Trailers: Air springs are commonly employed in heavy-duty vehicles, including commercial trucks and trailers. They help to improve load-carrying capacity, stability, and ride comfort. Air suspension systems allow for easy height adjustments, leveling, and load distribution, especially in applications where the weight of the cargo changes frequently.
- Commercial Aviation: Air springs are utilized in the aerospace industry, specifically in the landing gear of commercial aircraft. These airbags act as shock absorbers during landing and provide a smooth touchdown. They help to minimize vibrations, reduce stress on the airframe, and protect passengers and cargo.
- Rail and Transit Systems: Air springs are found in trains and other rail vehicles to enhance ride quality and passenger comfort. They absorb vibrations and shocks from the track, resulting in a smoother and quieter journey. Air suspension systems are also used in overhead wire maintenance vehicles to maintain a constant contact pressure with the catenary system.
- Medical Equipment: Air springs have medical applications as well. They are used in hospital beds, operating tables, and imaging equipment to provide adjustable support and positioning. Air springs ensure patient comfort, reduce the risk of pressure sores, and enable precise adjustments during medical procedures.
Application | Benefits of Air Springs |
---|---|
Automotive Industry | Improved ride quality, stability, and load capacity |
Industrial Machinery | Vibration isolation, noise reduction, and protection against shock forces |
Heavy-Duty Vehicles and Trailers | Enhanced load-carrying capacity, stability, and easy height adjustments |
Commercial Aviation | Smooth landing, reduced vibrations, and protection of aircraft structure |
Rail and Transit Systems | Improved ride quality, reduced noise, and constant contact pressure |
Medical Equipment | Adjustable support, patient comfort, and precise positioning |
These are just a few examples of the common applications of air springs. Their versatility, reliability, and ability to adapt to different environments make them valuable components in numerous industries. Whether it’s improving vehicle performance, enhancing industrial processes, or ensuring passenger comfort, air springs continue to play a crucial role in various applications.
Maintenance and care for air springs
The maintenance and care of air springs are crucial for ensuring their longevity and optimal performance. By properly maintaining and caring for your air springs, you can increase their lifespan and reduce the chances of premature failure or issues. In this blog post, we will discuss some essential maintenance tips and techniques, as well as the necessary care for air springs.
One of the most important aspects of maintaining air springs is regular inspection. Periodically checking the air springs for any signs of wear and tear, leaks, or damage is vital. Look for cracks, punctures, or other visible signs of deterioration. If you notice any issues, it is crucial to address them promptly. Ignoring small problems can lead to significant issues and can even compromise the safety of your vehicle.
Another crucial aspect of care and maintenance for air springs is keeping them clean and free from debris. Over time, dirt, dust, and other contaminants can accumulate on the surface of the air springs. Cleaning them regularly will help prevent the build-up of grime and debris, which can hinder their performance and potentially cause damage. Use a mild soap solution and a soft brush to clean the air springs thoroughly. Avoid using abrasive materials or harsh chemicals as they can damage the springs.
- Regular inspection for wear and tear, leaks, or damage
- Keep air springs clean and free from debris
- Ensure proper inflation levels of the air springs
- Follow manufacturer’s guidelines for maintenance and care
Proper inflation is essential for the optimal performance of air springs. It is vital to monitor and maintain the correct air pressure levels in the springs. Fluctuations in temperature, changes in load, or extended periods of non-use can cause changes in air pressure. Check the inflation levels regularly using a pressure gauge and make adjustments as needed. Keeping the air springs properly inflated will not only enhance performance but also prevent excessive stress and damage to the springs.
Benefits of Regular Maintenance and Care for Air Springs |
---|
Extended lifespan |
Improved performance and comfort |
Reduced risk of failures and breakdowns |
Enhanced safety |
Cost savings by avoiding expensive repairs or replacements |
In addition to regular inspection, cleaning, and proper inflation, it is essential to follow the manufacturer’s guidelines for maintenance and care. Each air spring may have specific instructions for lubrication, adjustment, or other maintenance tasks. Adhering to these guidelines will help ensure that you are taking the necessary steps to keep your air springs in optimal condition.
In conclusion, maintenance and care for air springs are vital for their longevity and performance. Regular inspection, cleaning, proper inflation, and following manufacturer’s guidelines are key aspects of maintaining air springs. By taking these steps, you can enjoy the benefits of extended lifespan, improved performance, enhanced safety, and cost savings in the long run.
Factors to consider when choosing air springs
When it comes to choosing the right air springs for your vehicle or industrial equipment, there are several important factors that you need to consider. Air springs, also known as air bags, are used in a variety of applications to provide support, cushioning, and load leveling. They are commonly found in vehicles, such as trucks, trailers, and buses, as well as in heavy-duty industrial equipment. Whether you are replacing worn-out air springs or considering upgrading your system, here are some key factors to keep in mind.
1. Load Capacity:
One of the most important factors to consider when choosing air springs is the load capacity. Each air spring has a specific load rating, which indicates the maximum weight it can support. It is crucial to select air springs that can safely handle the weight of your vehicle or equipment, taking into account any additional load that may be added.
2. Application:
Another important factor to consider is the specific application of the air springs. Air springs are designed for various applications, and it is essential to choose the right type that is compatible with your vehicle or equipment. Whether you need air springs for suspension systems, cab leveling, or seat support, selecting the appropriate type will ensure optimal performance and longevity.
3. Durability and Quality:
Considering durability and quality is crucial when selecting air springs. Look for air springs that are made from high-quality materials and have undergone rigorous testing. This will ensure that they can withstand heavy loads, extreme temperatures, and rough terrain. Investing in durable and reliable air springs will save you from frequent replacements and costly repairs in the long run.
4. Installation and Compatibility:
Before making a purchase, it is vital to consider the ease of installation and compatibility with your existing system. Check if the air springs come with clear installation instructions and if they are designed to fit your vehicle or equipment. Additionally, consider compatibility with the air compressor and control system, as well as any other components that are part of your suspension system.
5. Budget:
Lastly, it is essential to consider your budget when choosing air springs. While quality and durability should be a priority, it is also important to find a balance between cost and performance. Compare different brands and models, read customer reviews, and consider the warranty offered by the manufacturer. This will help you make an informed decision and ensure that you get the best value for your money.
By considering these factors when choosing air springs, you can ensure that you select the right ones that meet your specific requirements and provide optimal performance and durability. Remember, proper installation and regular maintenance are also essential for the longevity and performance of your air springs. Consult with experts if needed and follow the manufacturer’s guidelines to maximize the benefits of using air springs in your vehicle or industrial equipment.
Installation and replacement of air springs
When it comes to the installation and replacement of air springs, there are a few important things to keep in mind. Whether you are installing air springs for the first time or replacing an old and worn-out set, following the correct procedures is crucial for optimal performance and longevity.
1. Gather the necessary tools and equipment
Before you begin the installation or replacement process, it is essential to have all the required tools and equipment readily available. Some of the basic tools you may need include a wrench, socket set, jack stands, and a jack for lifting your vehicle. Additionally, make sure to check the manufacturer’s instructions for any specific tools or additional parts that may be required.
2. Follow the manufacturer’s instructions
Each air spring model may have its own unique installation and replacement instructions. It is essential to carefully read and follow the manufacturer’s guidelines to ensure a proper installation. These instructions often include step-by-step procedures, torque specifications, and any specific precautions that need to be taken.
3. Inspect and prepare the suspension components
Prior to installing the air springs, it is important to inspect the suspension components for any signs of damage or wear. Check for any loose or worn-out parts, such as bolts, bushings, or brackets, and replace them if necessary. Additionally, inspect the mounting areas where the air springs will be installed to ensure they are clean and free from any debris or corrosion.
4. Install and secure the air springs
Once you have prepared the suspension components, it is time to install the air springs. Start by positioning the air springs in the correct location, aligning them with the mounting holes or brackets. Use the provided hardware and follow the recommended torque specifications to secure the air springs firmly in place. Avoid over-tightening the bolts, as this could potentially damage the air springs or the suspension components.
5. Test and adjust the air springs
After the installation, it is crucial to test the air springs and make any necessary adjustments. Inflate the air springs to the recommended pressure according to the manufacturer’s instructions. Check for any leaks or abnormal noises, and ensure that the vehicle’s ride height is within the specified range. If adjustments are needed, follow the guidelines provided by the manufacturer to properly adjust the air springs.
Conclusion
Properly installing and replacing air springs is essential for maintaining the performance and functionality of your vehicle’s suspension system. By following the manufacturer’s instructions, conducting thorough inspections, and using the correct tools, you can ensure a successful installation or replacement process. Regular maintenance and care of your air springs will also contribute to their longevity and optimal performance.