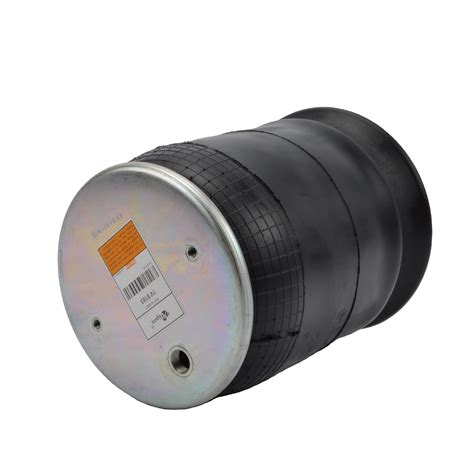
Air springs, also known as airbags or pneumatic springs, are a type of suspension system widely used in various industries. In this blog post, we will explore the significance of air springs and their numerous benefits. Additionally, we will delve into the manufacturing process of air springs, including the key factors to consider when choosing an air spring manufacturer. Moreover, we will discuss the importance of quality control measures in air spring production and highlight the technological advancements and industry trends driving innovation in this field. Whether you are a consumer or a business owner, this comprehensive guide will provide valuable insights into the world of air spring manufacturing.
What are air springs?
An air spring, also known as an airbag or air suspension, is a type of vehicle suspension system that uses air as the primary source of support. It is designed to replace traditional steel springs and provide a smoother, more comfortable ride. Air springs are typically made of reinforced rubber or synthetic materials, and they are used in a variety of applications, including cars, trucks, buses, and trailers.
One of the primary benefits of air springs is their adjustability. By varying the amount of air pressure inside the spring, the ride height and stiffness of the suspension can be easily modified. This allows for greater control and customization, depending on the load and driving conditions. It also helps to improve vehicle stability and handling.
Another important advantage of air springs is their ability to support heavy loads. Unlike traditional steel springs, which can often sag or become damaged under extreme weight, air springs can be inflated to provide the necessary support. This makes them particularly useful in commercial vehicles or applications that require frequent load changes.
- Adjustability: Air springs can be easily customized by varying the air pressure, allowing for greater control and comfort.
- Load Support: Air springs excel at supporting heavy loads, making them ideal for commercial vehicles and applications with frequent load changes.
- Enhanced Stability: Air springs improve vehicle stability and handling by maintaining a consistent ride height.
Advantages of Air Springs | Disadvantages of Air Springs |
---|---|
– Adjustable ride height- Smooth and comfortable ride- Improved load-carrying capacity- Enhanced vehicle stability- Easy to install and replace | – Higher initial cost- Requires periodic maintenance- Vulnerable to punctures or leaks- More complex system compared to traditional springs |
Why are air springs important?
Air springs, also known as air suspension systems, play a vital role in various industries and applications. These innovative and versatile devices offer numerous benefits and are gaining increasing importance in modern technology. Economy, safety, and comfort are among the key factors that make air springs an essential component in many vehicles and industrial machinery.
One of the primary reasons why air springs are important is their ability to provide a smooth and comfortable ride. The air-filled chambers in these springs act as cushions, effectively absorbing and dampening shocks and vibrations. This is particularly crucial for heavy-duty vehicles such as trucks, buses, and commercial aircraft, where ensuring passenger comfort and minimizing the impact of bumps and rough terrains are paramount.
In addition to enhancing ride comfort, air springs also contribute to improved safety. By maintaining consistent vehicle height and preventing sagging or tilting, they optimize the handling and stability of vehicles. This is especially critical in emergency maneuvers or challenging road conditions, where a balanced and controlled ride can help prevent accidents and maintain optimal tire contact with the road surface.
Furthermore, air springs offer a higher load-carrying capacity compared to traditional coil or leaf springs. They can bear heavy loads without compromising performance or stability, making them indispensable in various industrial applications. From heavy machinery used in construction and mining to cargo transportation vehicles, air springs enable efficient load distribution and ensure the longevity of the equipment.
Another key advantage of air springs is their adjustability. By altering the air pressure in the chambers, the stiffness and height of the suspension can be modified, allowing for dynamic control depending on the load, road conditions, or user preferences. This versatility makes air springs ideal for a wide range of applications, from passenger cars that can switch between comfort and sport modes to specialized vehicles that require adaptable suspension systems.
In summary, air springs are important due to their ability to provide a comfortable ride, improve safety, handle heavy loads, and offer adjustable suspension settings. Whether in vehicles or industrial machinery, these devices contribute significantly to enhancing performance, efficiency, and overall user experience. Choosing the right air spring manufacturer that provides reliable quality, advanced technological features, and adheres to stringent quality control processes is essential to maximize the benefits of air springs.
List of benefits of air springs:
- Smooth and comfortable ride
- Enhanced vehicle handling and stability
- Higher load-carrying capacity
- Adjustable suspension settings
Table comparing air springs to other suspension systems:
Suspension System | Benefits |
---|---|
Coil Springs | Simple design, cost-effective |
Leaf Springs | High load capacity, rugged |
Air Springs | Smooth ride, adjustability, increased safety |
The benefits of using air springs
The benefits of using air springs in various industries are numerous. Air springs, also known as air suspension systems, are devices that use compressed air to provide support, cushioning, and vibration isolation in a wide range of applications. These innovative systems offer several advantages over traditional mechanical springs and have become a popular choice for many professionals in different industries.
One of the primary benefits of using air springs is their adjustability. Unlike mechanical springs, which have a fixed stiffness, air springs can be easily adjusted to accommodate different loads and weight distributions. By simply adjusting the air pressure, the stiffness of the springs can be altered, allowing for precise control over the vehicle or equipment’s suspension. This adaptability makes air springs ideal for applications where load capacity varies or where frequent adjustments are necessary.
Another significant advantage of air springs is their superior ride comfort. The nature of the air-filled chamber allows air springs to provide a smooth and comfortable ride by absorbing shocks and vibrations. The compressed air inside the springs acts as a buffer, reducing the impact of bumps and uneven surfaces on the vehicle or equipment. This not only improves the comfort of passengers or operators but also helps protect valuable cargo from damage.
Furthermore, air springs offer enhanced load-carrying capabilities. Due to their adjustable nature and ability to distribute weight evenly, air springs can handle heavy loads with ease. This makes them particularly valuable in applications such as trucking, recreational vehicles, and heavy machinery. With air springs, professionals can ensure that their vehicles or equipment can carry substantial loads without compromising stability, safety, or performance.
- Adjustability to accommodate different loads and weight distributions
- Superior ride comfort by absorbing shocks and vibrations
- Enhanced load-carrying capabilities to handle heavy loads
Benefits of Air Springs | ||
---|---|---|
Adjustability | Superior ride comfort | Enhanced load-carrying capabilities |
How are air springs manufactured?
When it comes to manufacturing air springs, there are several key steps and processes involved. These specialized components are essential in many industries and applications, providing cushioning, vibration isolation, and load support. In this blog post, we will explore the manufacturing process of air springs and the various techniques and technologies used to create these crucial elements.
Firstly, one of the main components of an air spring is the rubber bladder. This bladder is responsible for holding and compressing the air within the spring. To manufacture the bladder, high-quality rubber material is selected, ensuring durability and flexibility. The rubber is cut into the desired shape and then molded using heat and pressure. The molding process creates a seamless and airtight bladder, capable of withstanding high levels of pressure and long-term use.
Another important aspect of air spring manufacturing is the design and construction of the end plates. These plates are typically made from strong and durable materials such as steel or aluminum. They are designed to securely hold the bladder in place and provide the necessary connection points for installation. The end plates are manufactured using various techniques such as cutting, bending, and welding. The use of high-quality materials and robust construction ensures the longevity and performance of the air spring assembly.
- High-quality rubber material
- Seamless and airtight bladder
- Strong and durable end plates
- Various manufacturing techniques
Manufacturing Step | Description |
---|---|
Bladder Creation | The rubber bladder is cut and molded into the desired shape using heat and pressure. |
End Plate Construction | The end plates are manufactured using techniques such as cutting, bending, and welding. |
Assembly | The bladder is securely connected to the end plates, creating the final air spring assembly. |
Testing | The manufactured air spring undergoes rigorous testing to ensure quality and functionality. |
Once the bladder and end plates are ready, the assembly process begins. The bladder is carefully and securely connected to the end plates, creating the final air spring assembly. This step requires precision and attention to detail to ensure a proper seal and airtight connection. Skilled technicians and specialized tools are often used to complete this assembly process efficiently.
Finally, to ensure the quality and functionality of the manufactured air springs, rigorous testing is conducted. These tests include evaluating factors such as pressure resistance, load-bearing capacity, and durability. Any air springs that do not meet the specified standards are rejected and sent back for further adjustments or remanufacturing.
In conclusion, the manufacturing process of air springs involves intricate steps and techniques to create high-quality and reliable components. From the creation of the rubber bladder to the construction of the end plates, every aspect of the manufacturing process contributes to the performance and longevity of the air spring assembly. Through careful design, precise manufacturing, and thorough testing, air spring manufacturers produce products that meet the demanding requirements of various industries and applications.
Choosing the right air spring manufacturer
When it comes to air springs, choosing the right manufacturer is crucial for ensuring quality, performance, and reliability. Air springs, also known as air suspension systems, are used in various industries and applications to provide smooth and comfortable ride, reduce vibration and noise, and improve overall vehicle stability.
Before selecting an air spring manufacturer, it is important to consider several factors that will help you make an informed decision. One of the key factors to look for is the experience and expertise of the manufacturer. A reputable and established manufacturer with years of experience in air spring manufacturing is more likely to produce high-quality products that meet your specific requirements.
Another important aspect to consider is the range of products and customization options offered by the manufacturer. Different industries and applications have different air spring needs, so it is essential to find a manufacturer that can provide a wide range of options to suit your specific requirements. Whether you need air springs for trucks, trailers, buses, or industrial equipment, the manufacturer should be able to offer customization options to meet your unique needs.
- Product quality and durability: Look for manufacturers that have strict quality control processes in place. The air springs should be made of high-quality materials and undergo thorough testing to ensure durability and reliability.
- Technical support and after-sales service: A reliable manufacturer should offer technical support and assistance, as well as reliable after-sales service. This ensures that any issues or concerns can be addressed promptly and professionally.
- Industry certifications and standards: Check if the manufacturer complies with industry standards and holds relevant certifications. This provides assurance that the air springs meet quality and safety requirements.
Lastly, consider the manufacturer’s reputation and customer reviews. Look for testimonials or reviews from other customers who have used their air springs. Positive feedback and a good reputation in the industry are indicators of a manufacturer’s commitment to customer satisfaction.
Key Features to Consider when Choosing an Air Spring Manufacturer: |
---|
Experience and expertise |
Range of products and customization options |
Product quality and durability |
Technical support and after-sales service |
Industry certifications and standards |
Reputation and customer reviews |
Choosing the right air spring manufacturer is a decision that can greatly impact the performance and reliability of your air suspension system. By considering the factors mentioned above and conducting thorough research, you can select a manufacturer that meets your specific needs and ensures the highest quality air springs for your application.
The key features to look for in an air spring manufacturer
When it comes to choosing an air spring manufacturer, there are several key features that you should look for. These features can make a significant difference in the quality and performance of the air springs you purchase. By considering these factors, you can ensure that you are selecting a reliable and reputable manufacturer that meets your specific needs.
Quality: One of the most important features to look for in an air spring manufacturer is a commitment to quality. Quality should be evident not only in the final product but also in the materials used, the manufacturing processes employed, and the overall attention to detail. A manufacturer that prioritizes quality will have strict quality control measures in place to ensure that each air spring meets the necessary standards.
Experience and Expertise: It is crucial to consider the experience and expertise of the air spring manufacturer. Look for a manufacturer that has been in the industry for a considerable amount of time and has a proven track record of producing high-quality air springs. An experienced manufacturer will have a deep understanding of the technology, materials, and processes involved in air spring manufacturing, which can result in superior products.
Customization Options: Another feature to consider is the manufacturer’s ability to offer customization options. Different applications may require specific specifications or design features, and a manufacturer that can accommodate these requirements can be highly beneficial. Whether it’s adjusting dimensions, load capacities, or incorporating specialized features, a manufacturer that offers customization options can provide air springs tailored to your needs.
- High-quality materials
- Reliable and efficient manufacturing processes
- Commitment to quality control
- Excellent customer support and service
- Ability to meet specific requirements and customization
Feature | Importance |
---|---|
Quality | High |
Experience and Expertise | High |
Customization Options | Medium |
In summary, when looking for an air spring manufacturer, prioritize features such as quality, experience, and customization options. These key features will ensure that you are selecting a manufacturer that produces reliable and high-performance air springs. Additionally, consider other factors like the materials used, manufacturing processes, customer support, and the ability to meet your specific requirements. By considering all these aspects, you can choose the right air spring manufacturer for your needs.
Quality control processes in air spring manufacturing
Air springs play a crucial role in various industries, providing support and cushioning in a wide range of applications. But have you ever wondered how these essential components are manufactured? One of the key aspects of air spring production is quality control processes, which ensure that the final products meet the highest standards of performance and reliability. In this blog post, we will explore the importance of quality control in air spring manufacturing and the various processes involved.
1. Incoming Material Inspection: The first step in ensuring quality control is to thoroughly inspect the incoming materials. Raw materials such as rubber, fabric, and metal parts must meet specific specifications and standards. Any deviation from these requirements can lead to inferior air springs. Comprehensive checks are conducted on each component to ensure their suitability for further production.
2. Laboratory Testing: To guarantee the quality and performance of air springs, extensive laboratory testing is conducted. These tests evaluate various characteristics such as load capacity, compression resistance, durability, and temperature tolerance. By subjecting the springs to demanding conditions, manufacturers can identify any potential weaknesses and make necessary improvements in the design and production processes.
3. Production Line Inspections: Quality control is integrated into the production line itself. At every stage, skilled technicians conduct inspections to identify any defects or deviations. Automated systems and equipment are utilized to detect irregularities in the assembly process, ensuring that each air spring is manufactured accurately and consistently. By monitoring the production line closely, manufacturers can minimize errors and maintain high-quality standards.
4. Performance Testing: Before the air springs leave the production facility, they undergo rigorous performance testing. These tests simulate real-world scenarios to assess factors such as load-bearing capacity, vibration resistance, and leak-proof performance. By subjecting the air springs to demanding conditions, manufacturers can determine their reliability and functionality. Only products that pass these tests are deemed suitable for customer use.
As you can see, quality control processes in air spring manufacturing are comprehensive and vital to ensure the utmost quality in the final products. These processes involve inspections, laboratory testing, production line evaluations, and performance testing. The integration of these quality control measures guarantees that air springs meet customer requirements and perform exceptionally in various applications. So, whether you are using air springs in automotive, railway, or industrial systems, you can have confidence in their reliability thanks to these stringent quality control processes.
Technological advancements in air spring manufacturing
Technological advancements in air spring manufacturing have revolutionized the way these essential components are designed and created. With constant innovation and improvements, manufacturers have been able to develop air springs that offer enhanced performance, durability, and efficiency. The advancements in technology have not only made air springs more reliable but have also expanded their applications in various industries.
One of the key technological advancements in air spring manufacturing is the use of computer-aided design (CAD) software. This software allows manufacturers to create detailed 3D models of the air springs, providing a virtual representation of the final product. CAD software enables engineers to efficiently design and test different prototypes, resulting in the development of air springs with optimized performance characteristics.
Another significant advancement is the use of automation in the manufacturing process. Modern air spring manufacturing facilities are equipped with robotic systems that can perform repetitive tasks with high precision and efficiency. This automation not only increases productivity but also ensures consistent quality in every air spring produced. Manufacturers can now rely on automated machinery to handle complex manufacturing processes, such as molding, bonding, and assembly.
In addition to CAD software and automation, the introduction of advanced materials has also played a crucial role in the technological advancements in air spring manufacturing. Traditional rubber compounds have been replaced by innovative materials such as polyurethane, which offer improved durability, resistance to wear and tear, and enhanced load-carrying capacity. These materials have also allowed for the development of air springs that can withstand a wide range of environmental conditions, including extreme temperatures and corrosive substances.
The technological advancements in air spring manufacturing have not only improved the performance and durability of these components but have also resulted in cost savings and environmental benefits for industries that rely on them. By using advanced technology, manufacturers can reduce material waste, streamline production processes, and minimize energy consumption. Furthermore, the enhanced performance of air springs can lead to increased efficiency in various applications, such as automotive suspensions, industrial machinery, and transportation systems.
In conclusion, technological advancements have greatly influenced the manufacturing of air springs. The use of CAD software, automation, and advanced materials has revolutionized the design and production processes, resulting in air springs that offer superior performance, durability, and efficiency. These advancements have opened up new possibilities for various industries and have contributed to cost savings and environmental benefits. As technology continues to evolve, we can expect further innovations in air spring manufacturing, pushing the boundaries of what these essential components can achieve.
Industry trends and innovations in air spring manufacturing
In the rapidly evolving manufacturing industry, air springs have become an essential component in a wide range of applications. From automobiles to heavy machinery, the use of air springs offers numerous advantages in terms of performance, durability, and safety. As the demand for air springs continues to grow, so does the need for advancements and innovations in their manufacturing processes. In this blog post, we will explore the industry trends and innovations that are shaping the world of air spring manufacturing.
One of the key trends in air spring manufacturing is the shift towards the use of eco-friendly materials. With increasing concerns about environmental sustainability, manufacturers are exploring alternative materials that have a lower carbon footprint. For example, some companies have started using recycled rubber in the production of air springs, reducing the consumption of virgin materials and minimizing waste. This trend not only contributes to a greener manufacturing process but also aligns with the growing consumer demand for eco-friendly products.
Another significant trend in the industry is the integration of smart technology into air spring manufacturing. As automation and digitalization continue to revolutionize the manufacturing sector, air spring manufacturers are incorporating sensors and monitoring systems into their products. These smart air springs can collect data on performance, temperature, and pressure, allowing for real-time monitoring and predictive maintenance. By leveraging the power of data and connectivity, manufacturers can optimize the performance and lifespan of air springs, enhancing overall efficiency and reducing downtime.
Furthermore, advancements in manufacturing techniques are driving innovation in the air spring industry. Traditional manufacturing processes such as molding and vulcanization have been refined and optimized, leading to improved product quality and consistency. Additionally, the use of computer-aided design (CAD) and simulation software enables manufacturers to create complex air spring designs with enhanced precision and performance. These technological advancements not only improve the overall functionality of air springs but also enable manufacturers to meet the specific requirements and preferences of their customers.
In conclusion, the air spring manufacturing industry is witnessing a range of trends and innovations that are shaping the future of this crucial component. The adoption of eco-friendly materials, integration of smart technology, and advancements in manufacturing techniques are just a few examples of the rapid progress being made in this field. As the demand for air springs continues to grow, it is imperative for manufacturers to stay at the forefront of these trends and embrace innovations to meet the evolving needs of the market. By doing so, they can ensure the production of high-quality, efficient, and sustainable air springs that drive performance and enhance safety across various industries.